-
Wax Injection
The mould is filled with fluid wax. After cooling, the wax model is pushed from the mould using ejectors in the mould. A wax model will be formed with the same shape as the final cast piece
-
Wax Sprue Assembling
These wax moulds must assemble into a tree by heating the attachment point until it becomes fluid and sticks to a wax branch. This creates the casting mould. The top wax tree is equipped with a casting funnel through which steel will be poured later in the next process.
-
Shell building
A fire resistant coating is created by plunging the wax tree multiple times in a fluid sludge and then sprinkling it with ceramic powder. After the application of every ceramic layer, the casting mould must be dried in a drying chamber under atmosphere conditions
-
Knockout
The ceramic skin is removed from the steel casting moulds by breaking the shell with manual work hammer. This removes the majoirty of the ceramic. The cast pieces are sawed off or vibrated away from the steel tree.
-
Casting
The desired steel alloy is melted in a smelting furnace and brought up to a casting temperature of (approximately) 1600 oC. The hot mould is then removed from the kiln and poured full. Heating the ceramic mould prevents a thermal shock during casting. The fluid steel is poured into a hot mould, it takes some time before solidification.
-
Dewaxing
All ceramic layers have been dried; the wax in the ceramic mould is melted in an autoclave using steam. This is why this process is called the lost wax casting method: the wax model disappears; the product shape is taken over by the ceramic coating.
-
Cut Off
The steel is cut away from the tree using a grinding process.
-
Griding & Mirror Finishing
Any edges are deburred off the casted pieces and sanded.
-
Vibratory Finishing
The final production process is vibratory finishing. The vibratory finishing process is used to deburr, radius, descale, burnish, clean, and brighten.
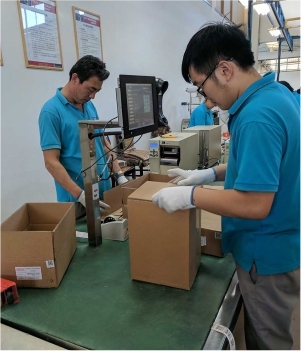
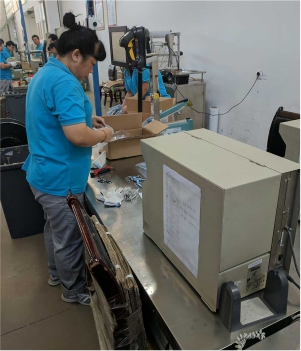
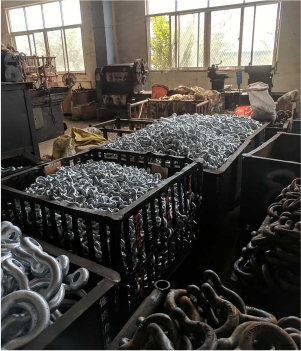
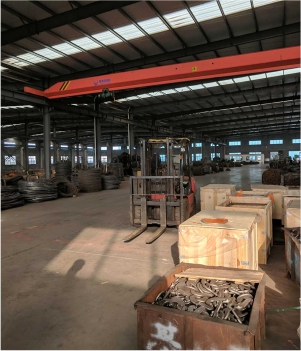
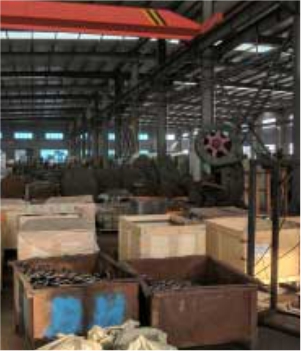
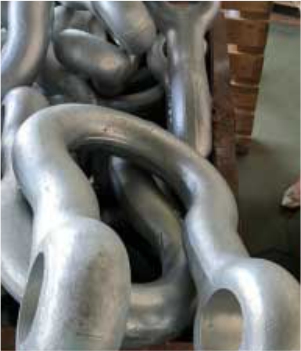
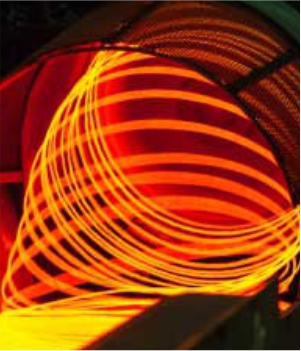